When selecting the ideal caster wheel for your specific needs, the decision between a cast iron wheel core and an aluminum wheel core is crucial.
Both materials offer unique advantages and considerations that should be carefully weighed. In this blog post, we’ll explore the pros and cons of cast iron and aluminum wheel cores, helping you make an informed decision for your caster wheels.
Aspect | Cast Iron Wheel | Aluminum Wheel |
---|---|---|
Material | Cast Iron Alloy | Aluminum Alloy |
Weight | Heavier | Lighter |
Heat Dissipation | Retains heat | Better heat dissipation |
Durability | Durable | Durable |
Corrosion Resistance | Susceptible to corrosion | Corrosion-resistant |
Brake Performance | May cause brake fade | Improved brake performance |
Fuel Efficiency | Lower fuel efficiency | Higher fuel efficiency |
Handling Performance | Reduced agility | Improved agility |
Aesthetics | Typically less attractive | Modern and sleek appearance |
Cost | Lower cost | Higher cost |
Caster iron wheel
Cast Iron Wheel Core: Strength and Durability for Heavy Loads
Cast iron wheel cores are known for their exceptional strength and durability, making them ideal for applications that involve heavy loads and demanding industrial environments. They are commonly used in conjunction with polyurethane wheels, as the porous nature of cast iron makes it easier to bond materials.
Cast iron wheel cores exhibit excellent bonding capabilities, ensuring secure attachment to the wheel material. Moreover, they offer high impact resistance, making them suitable for rolling over abrasive surfaces and enduring potential impacts without damage.
The porous structure of cast iron also aids in dissipating heat effectively, making it a preferred choice for continuous-use applications where heat dissipation is critical. However, it’s important to consider that cast iron wheels are heavier, which may not be ideal if weight reduction is a priority for your application.
Aluminum Wheel Core: Lightweight and Corrosion-Resistant
MS Dual Wheel Aluminm Caster
Aluminum wheel cores excel in weight reduction applications, making them a preferred choice in industries where minimizing overall weight is crucial. The aviation industry, for example, benefits greatly from the lightweight nature of aluminum wheel cores.
Meeting weight requirements and floor pressure specifications are critical in aviation applications, and aluminum helps achieve these goals. Additionally, aluminum exhibits natural corrosion resistance properties, making it suitable for outdoor applications and environments prone to moisture. The corrosion resistance of aluminum wheels is also advantageous in wash-down applications, where steel or cast-iron wheels would corrode more rapidly.
It’s important to note that aluminum does not dissipate heat as efficiently as cast iron due to its density and thermal conductivity. Continuous use applications with high heat generation should be carefully evaluated, and consulting with a representative is recommended for such scenarios.
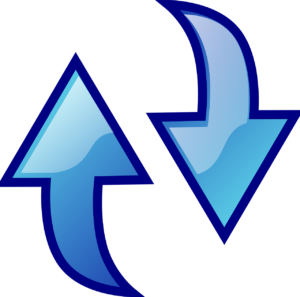
Trade-offs and Considerations:
There are trade-offs to consider when choosing between cast iron and aluminum wheel cores. Cast iron offers advantages such as load-bearing capacity, impact resistance, wear resistance, heat dissipation, and longevity, making it suitable for heavy-load and continuous-use applications.
On the other hand, aluminum offers benefits like weight reduction, corrosion resistance, and suitability for outdoor and wash-down applications. However, it may have limitations in load-bearing capacity, heat dissipation, and resistance to impacts compared to cast iron. Factors such as load, speed, duty cycle, environmental conditions, and customer preferences should be considered when selecting the ideal wheel core material.
Remember, the right wheel can change everything. Carefully considering the factors listed above, you can’t steer the wrong way! Consult with the material handling experts at Caster Concepts. Our experience and testing of casters in many different industrial applications can provide valuable insights into the performance and suitability of different wheel core materials for your specific application. The right material goes a long way.
No comment